A short week in the shop
Published 16 Dec 2019
This week was a short one shop wise, as I travelled to meet the rest of my family to say goodbye to my Gran, who passed away. As with my Grandad on the other side of my family that I similarly said goodbye to a few months ago, my Gran (who we always called Nanna) was another major influence on me; certainly in terms of my slightly silly sense of humour and that ability to see the funnier side of life. She was always buoyant in spirit to us grandkids, even when her own life was troubled, and I hope that spirit is something I can remember when things feel difficult for me.
The little time I did get in the shop this week was spent getting the commission neck that I fixed last week re-oiled and out the other side of finishing.
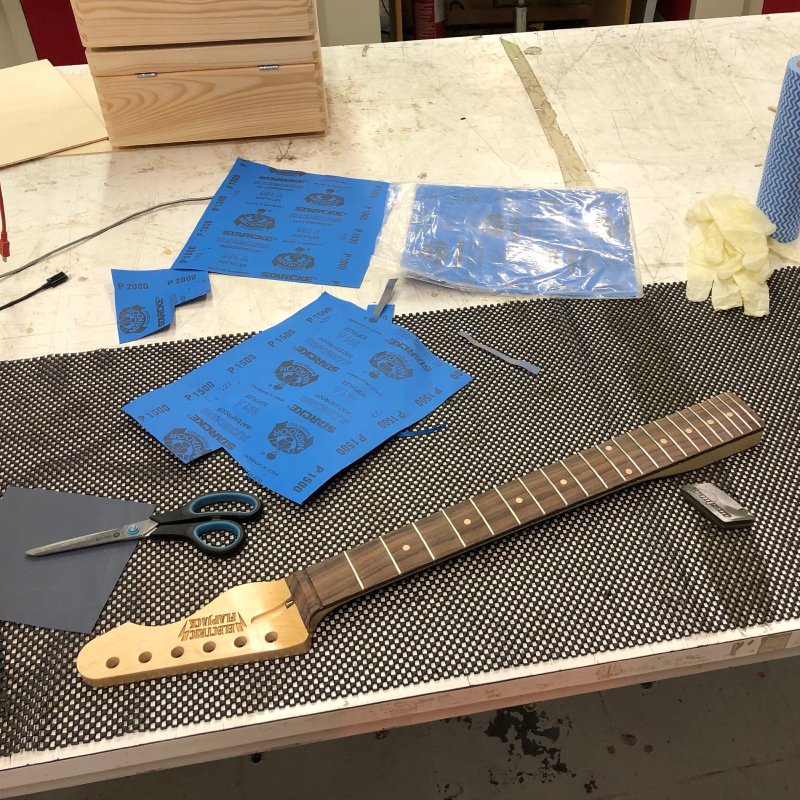
Last week I’d had to sand off the finish from the headstock to let me repair it, and started re-applying oil to those areas. At the start of the week I spotted another slight dent, which was really subtle, but once I’d seen it I couldn’t un-see it, so I had to also strip the oil on that spot, do the hot water trick (this one was sufficiently small hot water alone caused it to fill out again) and then re-oil that bit too.
To get the oil layer back up to match the rest of the finish I needed to work up to four coats. If nothing else did this wonders for my exercise levels as I had to cycle in and out to Makespace twice a day over the weekend to get this done quickly.
I also applied finish to the fretboard part of the neck, as thus far all the finishing had been on the maple part. The way rosewood is treated is different to how the maple is treated, and requires much less work thankfully - just a single coat of oil that is there to keep the wood moist rather than sealed. Over time this will need toped up, but gives a very different feel in terms of touch to the player.
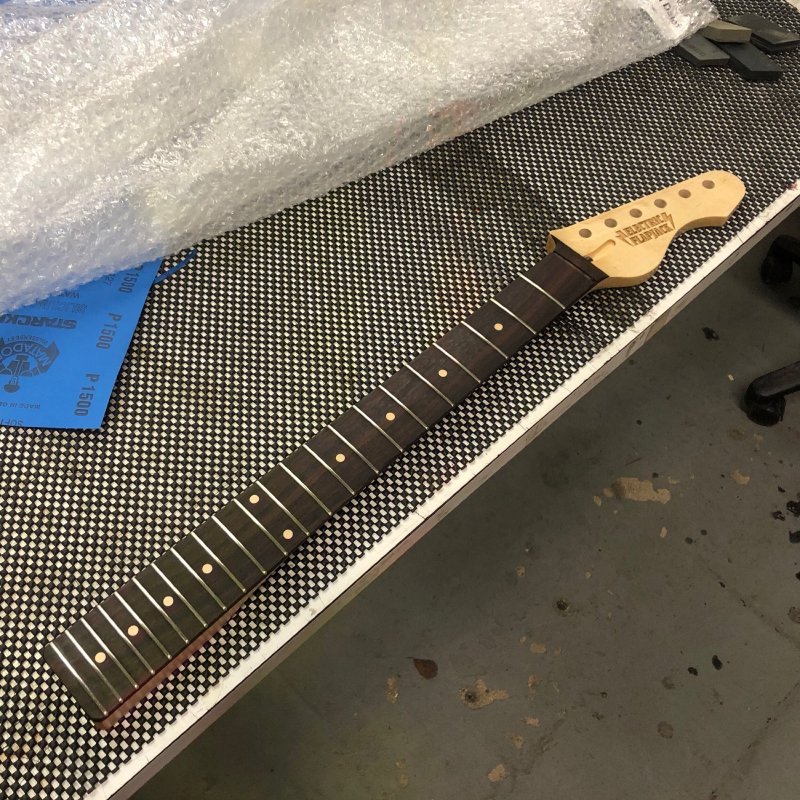
Before I oiled it I first re-polished the frets, to remove the tiny scratches they’d picked up in the fall and from where I’d inevitably rubbed them with sandpaper whilst tidying up the fretboard repairs. That done it was then a quick job to give it its single coat of oil.
Now the neck should be completed in terms of finish, so this week I get to put the neck on the body and it can move into a guitar case and I can breathe a sigh of relief about it being in places people might accidentally damage it (it’s kept out the way in Makespace, but after this last couple of weeks I’m really paranoid now).
The next task on this guitar will be (at last, as I’ve said this before) to make the pick-guard for it, so I can then get mounting everything else. I’ve been holding of making the pick guard until the body and neck were married together to check for perfect fit.
Whilst waiting for the oil to cure over the weekend I took my amp along for a quick service:
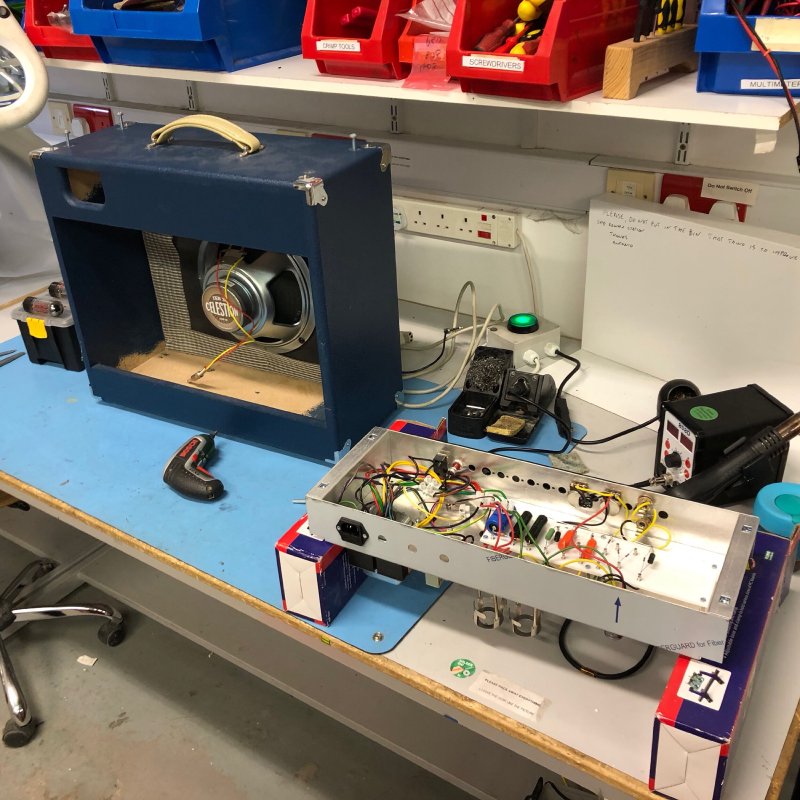
I made this amp almost two years ago now, and it’s used almost daily. Recently it’s been playing up a little though - slight static noises at times for particular notes. The most likely culprit is the valves, but before replacing them I wanted to just check that everything inside was good, and I’d noted that a screw holding the turret board in place had worked lose, as had one of the input jacks, so it was time to give it a quick once over.
With everything tightened up it’s still making occasional static noises on certain notes, so I’ve ordered replacement tubes and we’ll see if that clears it up.
I also did some workshop maintenance (along with Adrian, one the directors) at Makespace, looking at the thicknesser that someone had reported was scratching:
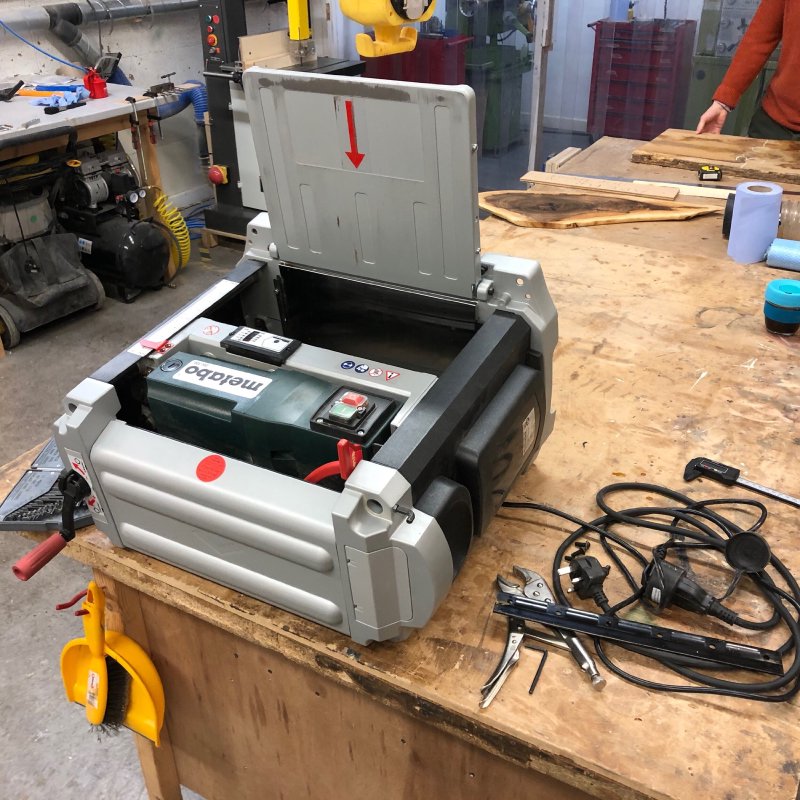
Indeed, we found someone had been running through material with metal fixings in it, which is somewhat vexing, as we go to great lengths in training telling people not to do that. Such is the nature of a shared workshop though: people sometimes ignore instructions like that, or hope to get away with it. It’s a difficult balance in a place like Makespace where you don’t want to be so draconian in rules as to put people off, but with something as powerful as the thicknesser you really don’t want people abusing the machine as that can lead to not just damaged materials but the machine becoming unsafe potentially.
In this case there was what looked like a nail head that had got stuck behind one of the cutting blades that was causing it to scratch material it was thicknessing, so we removed the blade and cleared that out, and sent out a reminder to people on the woes of reclaimed wood with workshop machines.