A chaotic week in the shop
Published 16 Sep 2019
This week was quite a chaotic one, for main two reasons, one good and one bad. Let’s get the bad one out the way: both my laptop and my primary backup source died on me within several days, and not in that order. I first noticed my laptop was sick early in the week where it’d just die every 5 minutes or so, particularly if I loaded graphics intensive apps such as Fusion 360 (though not exclusively). This was a major pain guitar build wise, as although I hand-build things, all my designs are in Fusion 360, so if I want to check measurements I need be able to access my laptop.
Whilst clearly frustrating, at first I wasn’t too concerned: laptop disks dying is to me the same as love is to Rick Astley: I’ve had my fair share of laptops (more specifically usually their disks) die on me, so I plan appropriately. I have a tendency to buy the a top-of-the-line laptop every 4 or 5 years then use it until they die rather than update something less good more regularly (this particular MacBook Pro was bought in mid 2014, so has had a good innings). Given I hold on to machines for a long time, I know that disks can also just fail randomly, so I always make sure I have a regular backup system. However, it unfortunately turned out that four days before my laptop started dying, the Apple Time Capsule I use as my primary backup/restore mechanism also had a disk failure. Two major failures in such a close period of time is rare, but does happen. I’ve no idea how old our Time Capsule is, but it must pre-date my MacBook Pro as I remember restoring my dead MacBook Air onto the Pro when I got it (as the Air had suffered a disk failure - you see a pattern here?).
Thankfully, because I know my businesses (both the software contracting I do to earn my keep and the guitar building business) rely on me being able to have all my data, I actually have a second regular backup system in place. As convenient as the Apple Time Capsule is when it works, it always felt a little fragile to bet your business on, particularly as Apple’s focus on the Mac has waned in recent years. Last year I bought a Synology NAS box and set that up with redundant disks so if any one disk in my NAS box dies I still have my data, and I combined the NAS with using Retrospect backup software to take care of not just my Mac but also my Windows partition that I need to use some times (something the Apple Time Capsule couldn’t do). At the time when I bought all this it seemed like a lot of money (easily a grand) for something you hope you’ll never have to use, but this week it demonstrated its value nicely.
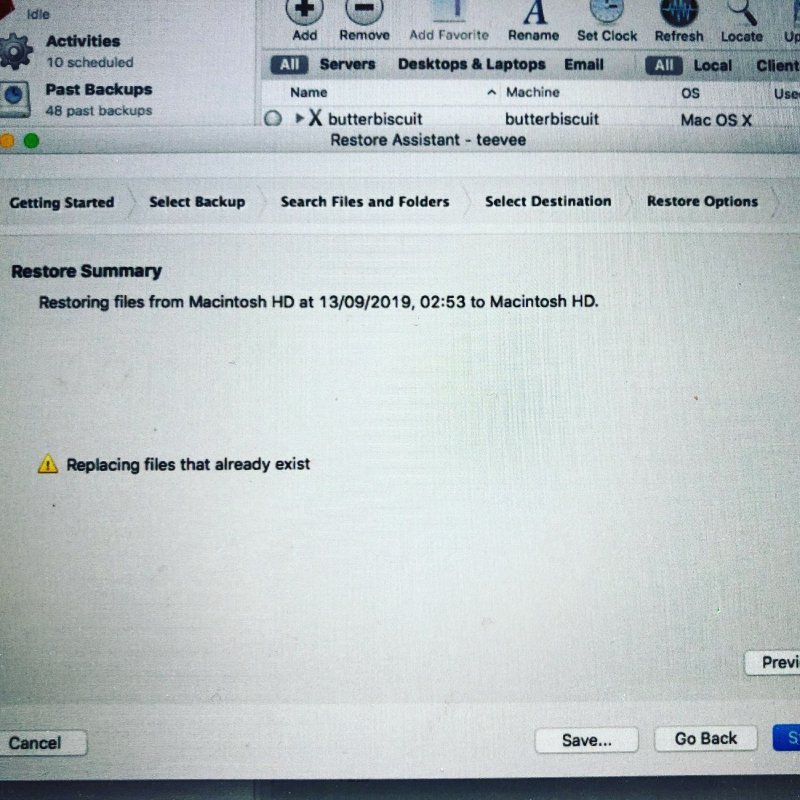
So after a few days downtime, I have a borrowed laptop (my other-half’s old laptop) and all my data back and I’m back in action. At some point in the very near future I’ll replace this with a new laptop, but having an old laptop for now lets me make a considered purchase not a panic purchase, which is good (particularly as I doubt I’ll be getting another Mac this time, but that’s another discussion for another blog).
Anyway. the moral of the tail is: have backups, and ensure they’re in good health, as things can go doubly wrong at times. Whilst sorting out backups often isn’t cheap, being able to restore your data and be back running after minimal downtime is priceless: this is at least my third machine failure where if I’d not had backups I’d have been sunk.
If you don’t want to buy and run your own backup infrastructure, then consider a cloud based service like Backblaze, which is relatively painless and will give you peace of mind.
It’s a little telling to me that although I’m making things by hand I’m still so reliant on being able to double check things and review numbers on my computer before cutting (measure, measure, cut). Over time I imagine I’ll get more of this down to muscle memory - how big is the headstock transition, etc. But for now I still have a strong level of paranoia for numbers and my desire to get everything just so.
The good chaos this week was having some filming done for a promo. My brother Tristan and his other-half Ket run a videography/photography company, which does a mix of music videos, weddings, and corporate gigs. In the past I’ve tried to make my own little videos of the guitars I make, but as a novice with high standards it always ends up becoming a massive time-sink. As fun as it is, I realise there’s better uses of my time, and I decided it was time to get the experts for some new videos.
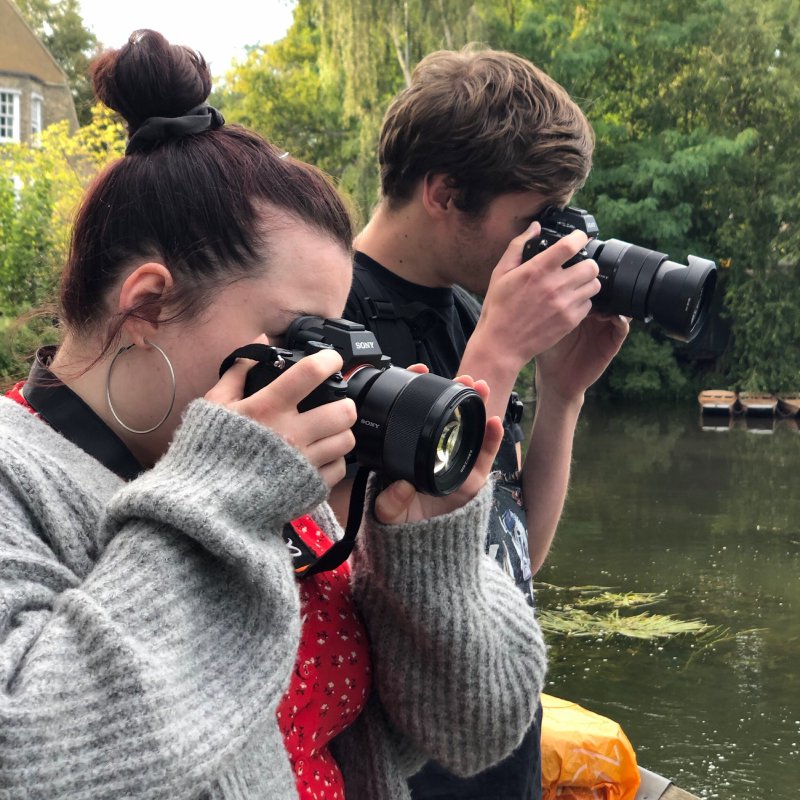
The pair had a corporate gig on in Cambridge this week, so they dovetailed me in after that. We had a day of shooting bits of guitar building in the Makespace workshop, some bits around Cambridge itself, and some interview footage. Tris also brought back down the guitar I built him quite a while ago just to have it checked up:
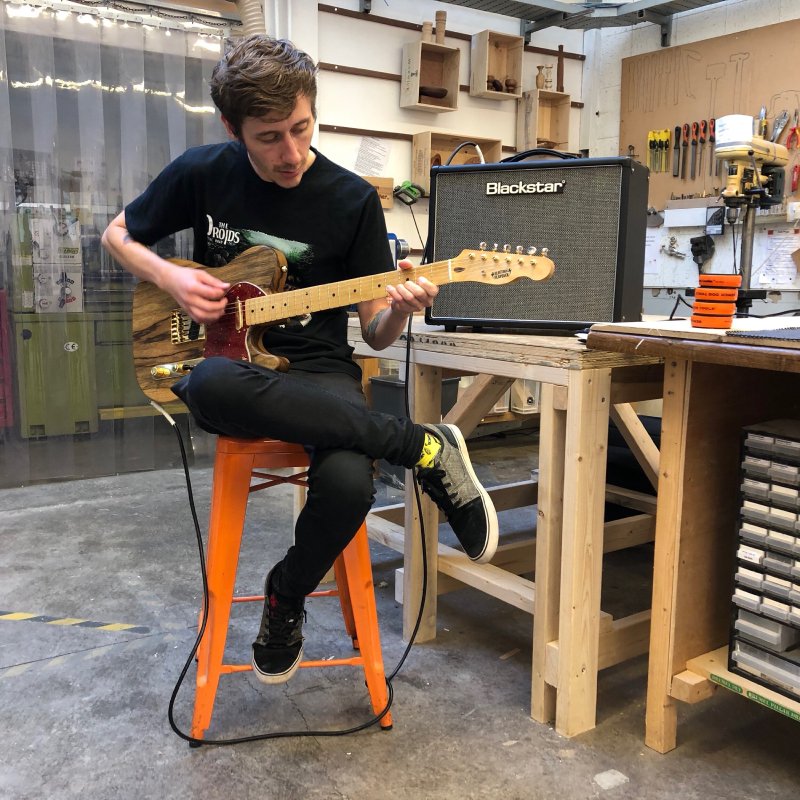
It was nice to see that beyond giving it a bit of a clean, there was nothing that needed tweaked, despite it seeing some serious action on stage and in recording studios over the last couple of years.
I’ve no idea what the promo footage will look like, it’ll be fun to find out when it eventually emerges: I’ve put my faith in Tris and Ket as the experts to come up with something suitable - there’s no point hiring people who know what they’re doing and micro-managing them. There’s a reason I’m paying them, and I’m happy to just let them do what they do well so I can get on with what I do well.
Beyond the chaos I did get some guitar progress done. I started the week as I ended last week, which was finishing the comfort carves on the bodies for guitars #10 and #6.
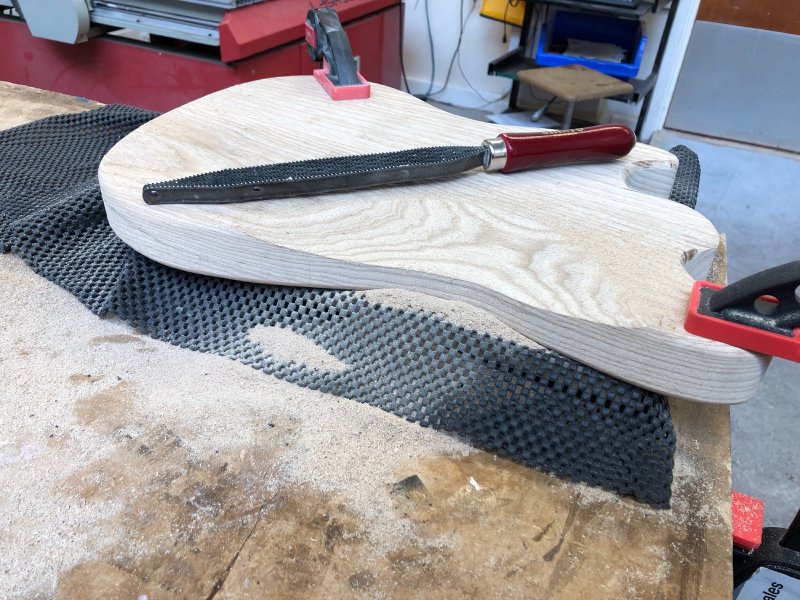
It’s a nice workout doing this by hand, but after an hour or two I was done. Lots of pencil guide lines are used to keep me on track, and then the rasp tooth marks are cleaned up using my random-orbital sander to give a nice smooth finish.
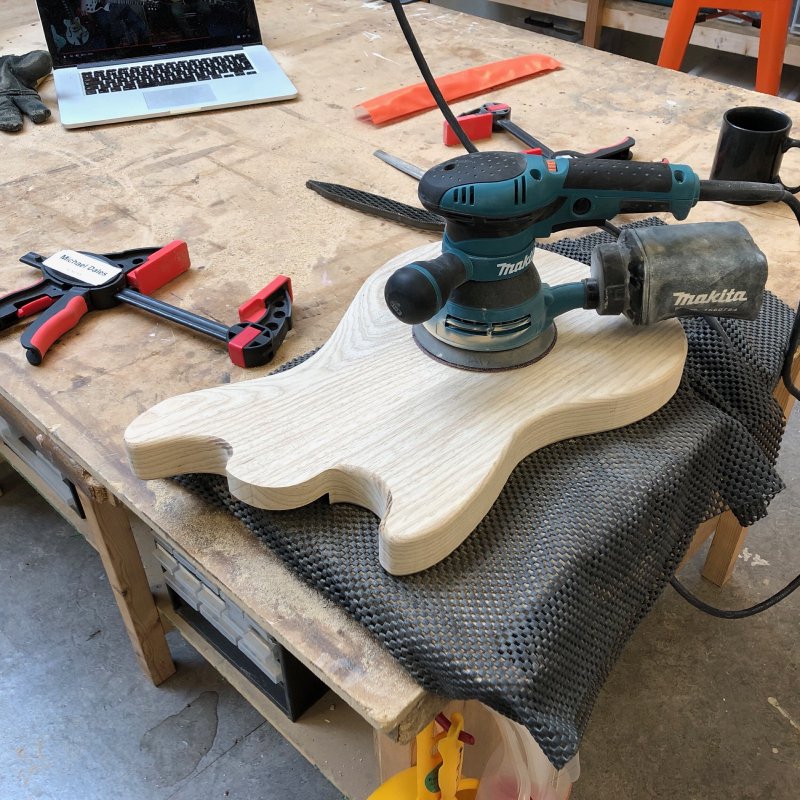
That means the bodies for #10 and #6 are now done bar the bridge mount holes, which I’ll do once I have the necks so I can make sure the bridge position is spot on.
Next, I moved the neck for #10 forward, although this was impacted by being laptop-less unfortunately. Last week I’d routed out the main body of the neck along with the truss rod cavity, and so this week I wanted to get that progressed along so I can glue on the fretboard. To do this, I first needed to make a jig to let me hold the neck parallel to the work table on the bandsaw and spindle sander, so it was an hour or so on the CNC Router to make the jig.
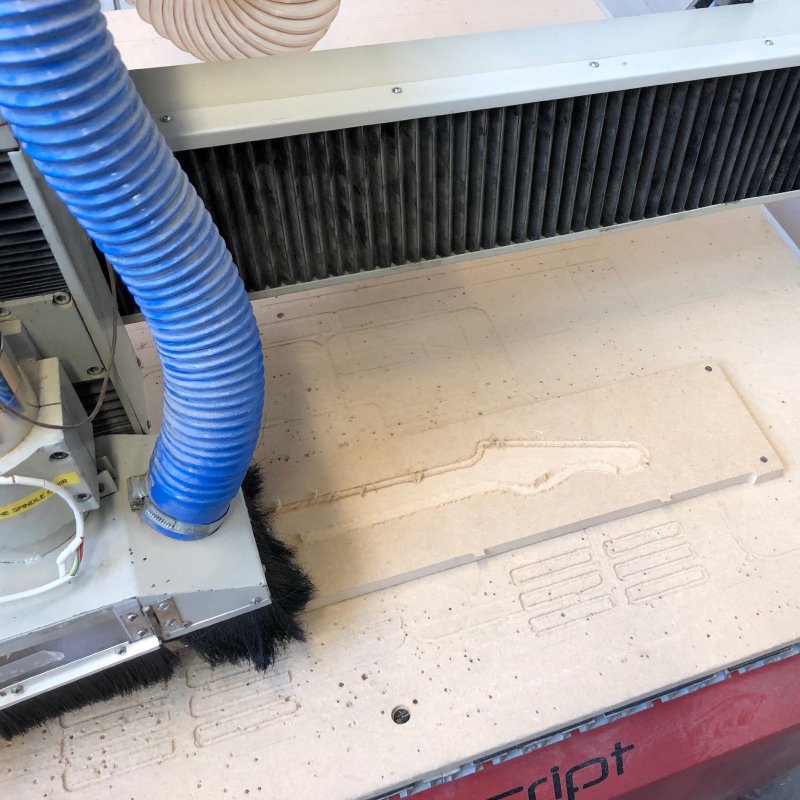
As I’ve said before (I think) whilst I don’t trust the CNC Router, the cost of it going wrong on MDF is very low, so I’m happy to make jigs like this on it, I’m just not willing to put actual guitar wood on there. As you can see, I have another jig just like it, as the Corvette build I’m using to pilot bits of technique is a left-hander.
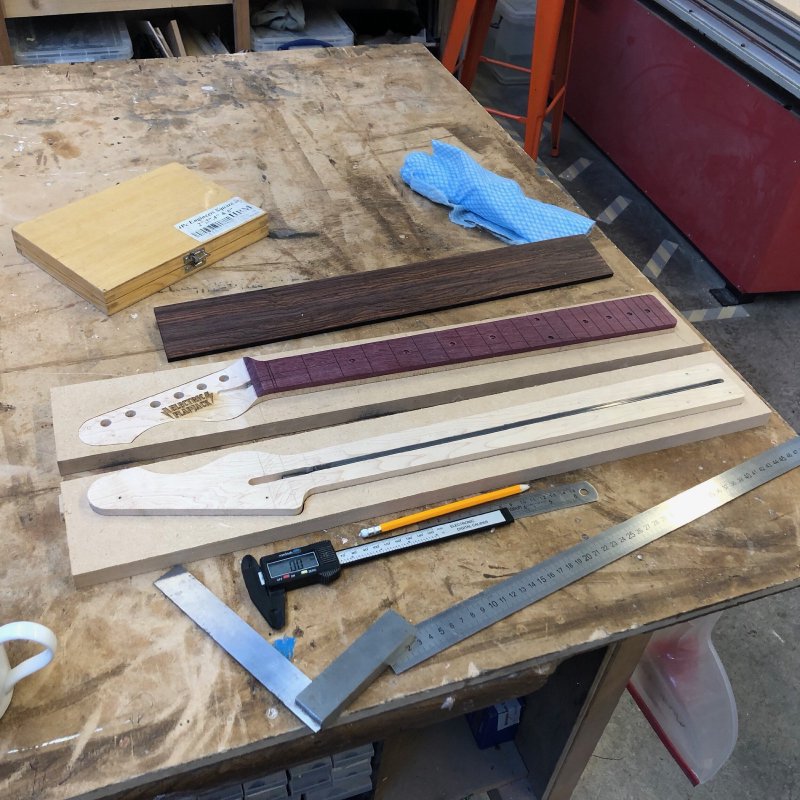
At this stage I got stuck for a while as I needed to check the measurements for where to remove the material from the headstock face and to start the transition curve up to the fretboard. When I realised my laptop restoration was going to be another day or so, I eventually loaded my Fusion design on my other-half’s new computer and took a photo of all the bits I needed!
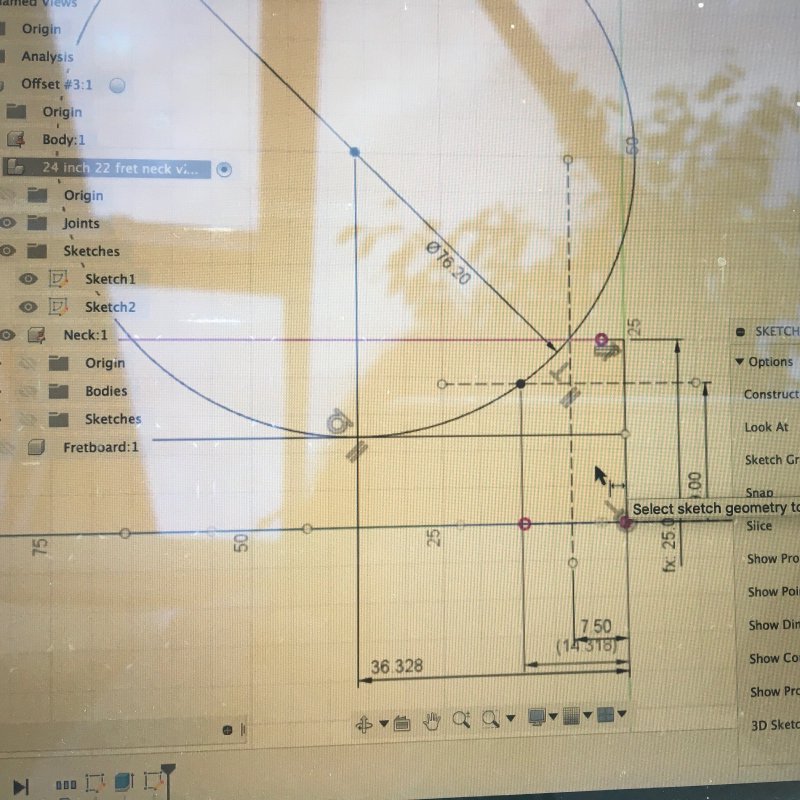
That let me get the positions right, and the reason I had the Corvette’s neck out at this point was to do a sanity check of the numbers given I was juggling so many things to get the numbers out. However, that done I was able to take the jig I’d made and run the neck through the bandsaw and the spindle sander to get the headstock shape made.
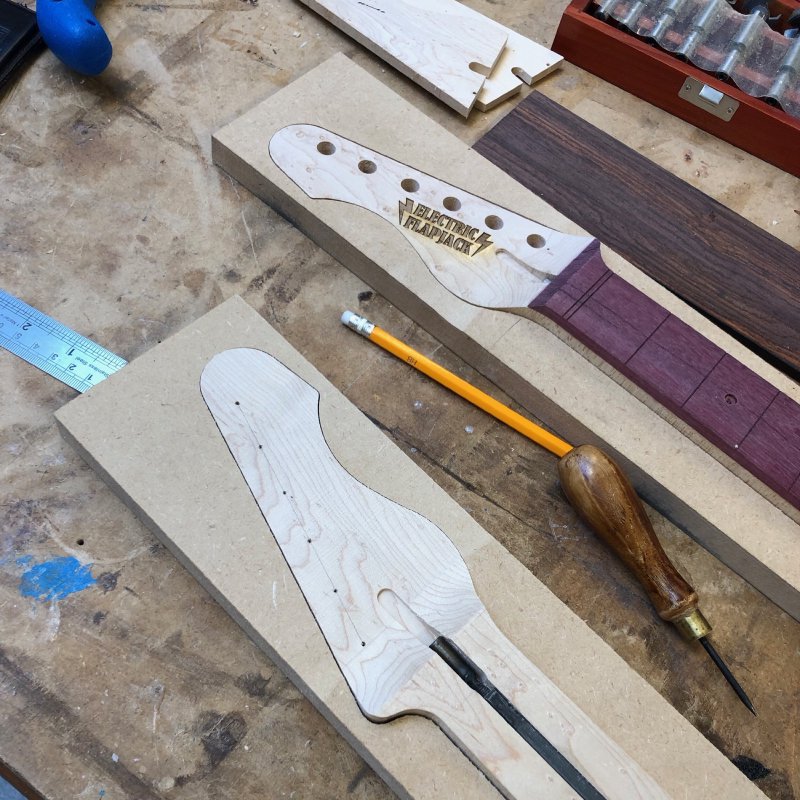
After that it was onto the pillar drill to make the holes for mounting the tuners, and with that done I was all but ready to glue the fretboard on, which is an absolutely stunning bit of indian rosewood with amazing colours to it.
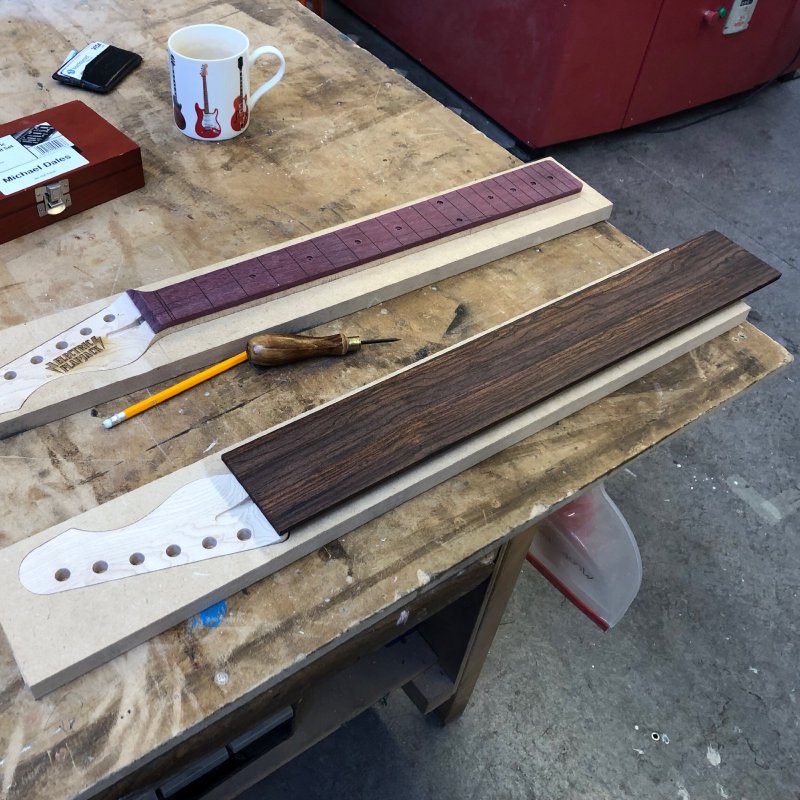
But alas someone beat me to all the Makespace clamps: whilst I have some of my own, not enough to do a full fretboard glue. So that’s now a job for early this coming week.
I did a bit of work on the Corvette too this week, mostly as I wanted to have it in a position where I could do some funky shots of a build being worked on for the promo filming. Despite the neck being ahead of the commissions, the body was a bit behind, so I did the routing of the edges to round them over for the filming. Here I was very pleased that my design was notably easier to route around than the Fender based designs of the commissions. For instance, if you look at the neck joint area on the back, I’ve rounded everything out to make it easier to reach the upper frets, but by keeping the lines as a continuous set of curves it was much easier to run the hand-router along in one smooth motion:
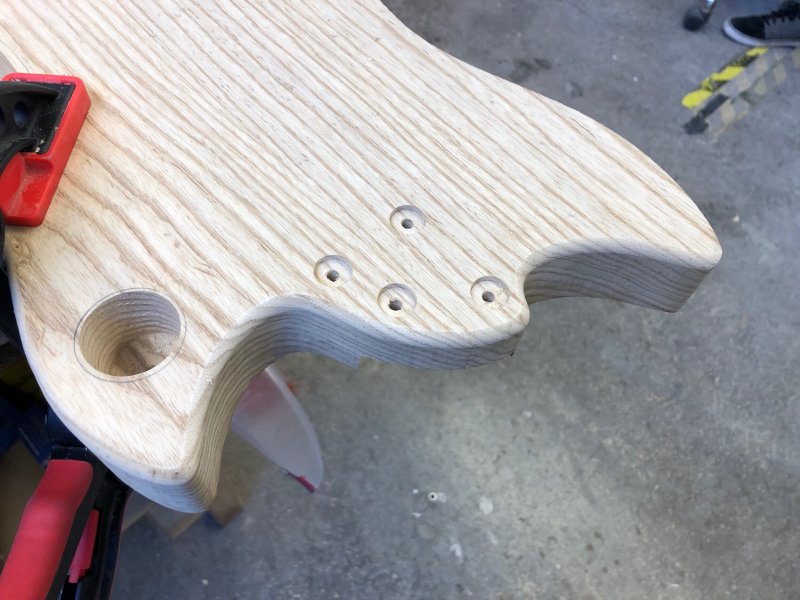
A nice case of trying to make things nicer for one use case actually making it easier to manufacture not harder as is often the case.
Another thing I worked on was laser etching the neck for the Corvette, and for this I made a tweak to my open source fretboard generator. Before it made circles where the inlays might be, but in practice I never used that option as I need a point not a circle when drilling, so I’d end up calculating all the inlay positions on the neck using a pencil and ruler. However, I was inspired by something I saw Jamie Swannell do when I helped him laser cut some things a couple of months ago, and I got my design generator to optionally also generate cross hairs where the inlays should be:
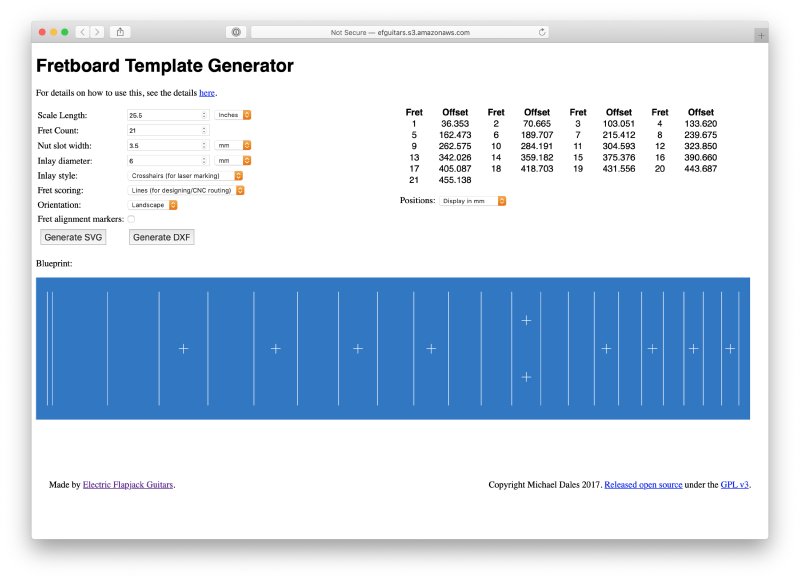
Now, I can take those cross hairs and when I laser etch the location of the fret slots I can also laser on a mark where the inlays should be:
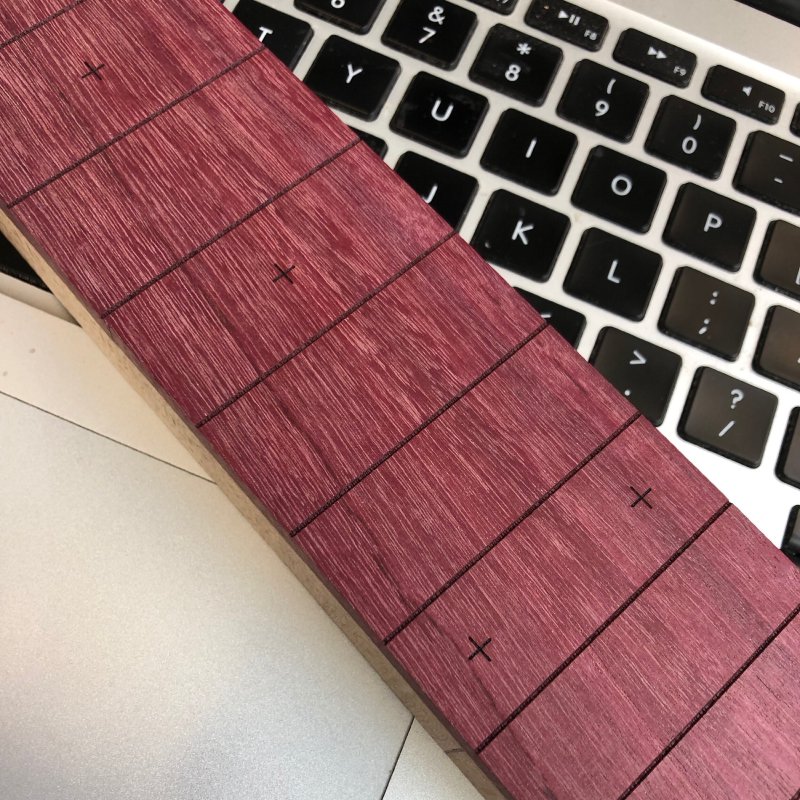
Because they’re burnt in here, not only do they give a visual reference, they’ll also guide the tip of my bradawl when I do to make the pilot hole for drilling the inlays. Another double whammy design wise. You can see in the pictures above when I was working on the neck for #10 that I was able to use these to drill out the inlay holes successfully.
Is this cheating for a hand built guitar? I don’t think so: firstly I hand wrote the code to generate it, so it’s still my work to get the inlay positions in the right place, and secondly it’s just making a guide mark, I still have to cut the inlays myself (as I do the fret slots when I use this technique).
I pushed the code changes for this so if you visit the open source section of this site you can play with the new functionality yourself!
I also laser etched the headstock, taking care to remember this is a left handed guitar, not a right handed one :)
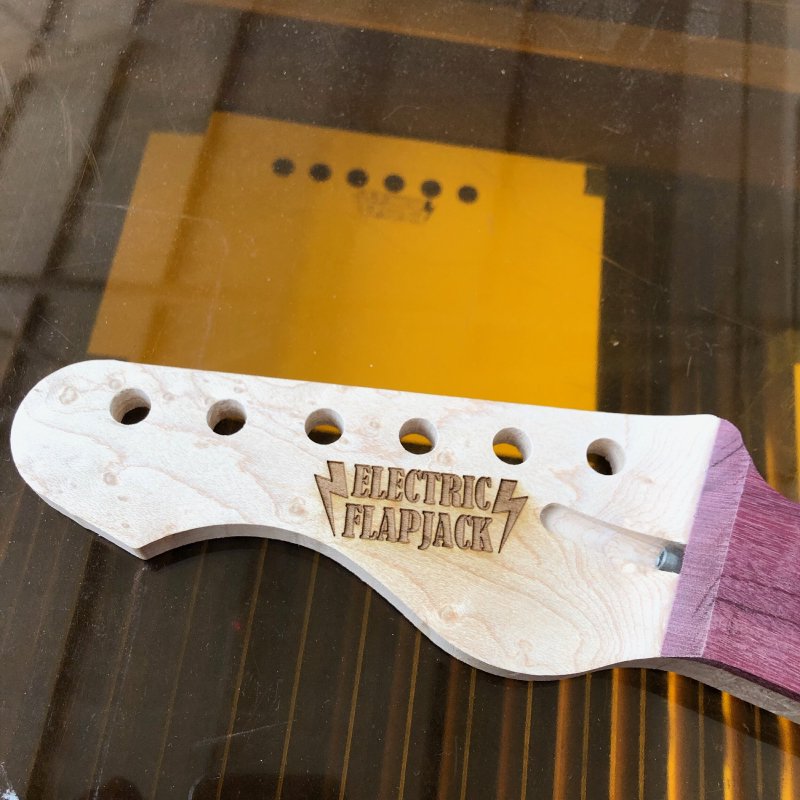
As ever, I had to do a lot of calibration burns. Even though I did this a couple of weeks ago for another neck, this maple seemed much tougher, and I had to use a slower burn to get the same level of material removed.
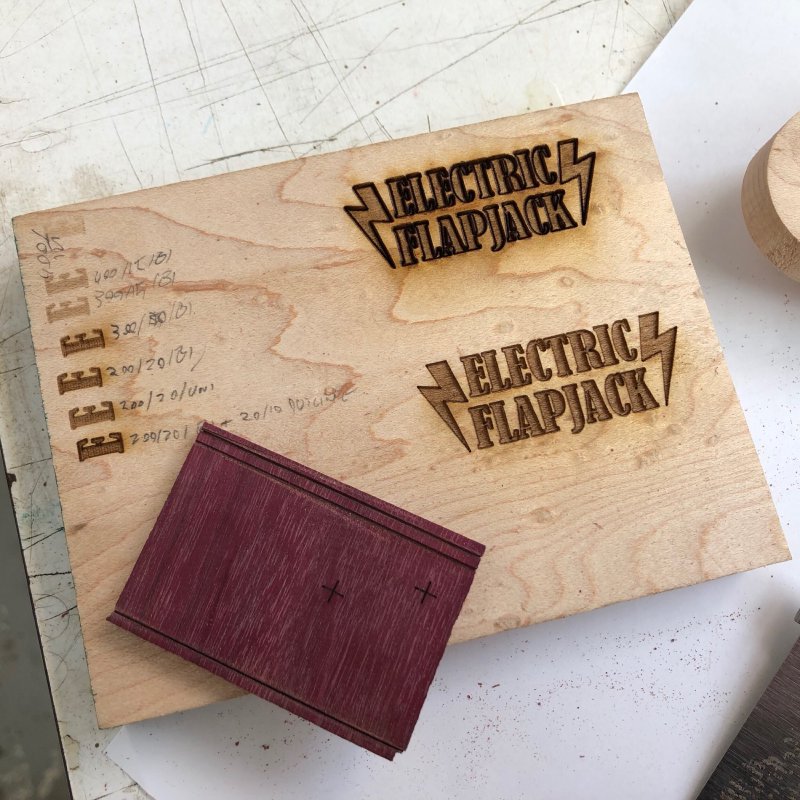
This is also why I don’t consider laser etching cheating: it’s still a very manual process getting everything set up just so.
The Corvette is starting to look like a guitar now. It still has a way to go, but for the first time it’s starting to look like the renderings I made several months ago, which is exciting.
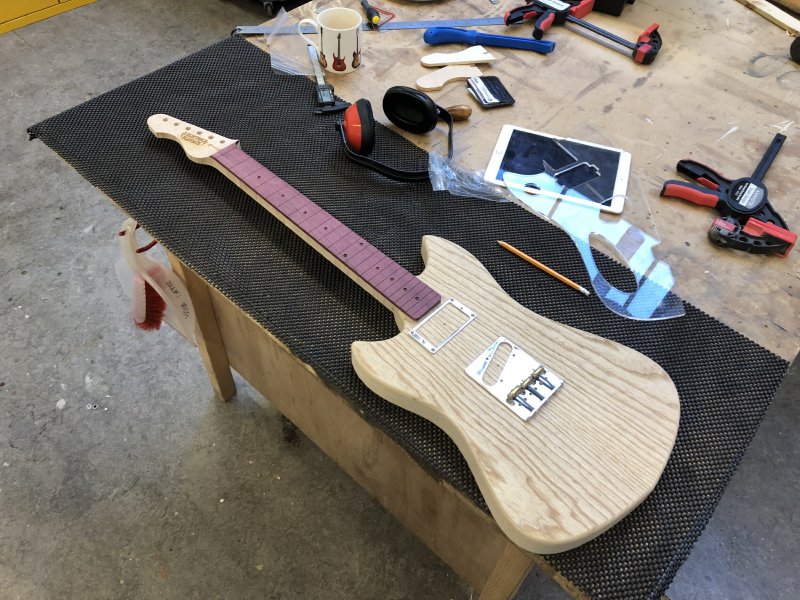
The last thing I recall doing was trying out some triangular needle-files that fellow Makespace workshop user kindly donated to me for use on adding a slight chamfer to the top edge of the fretslots:
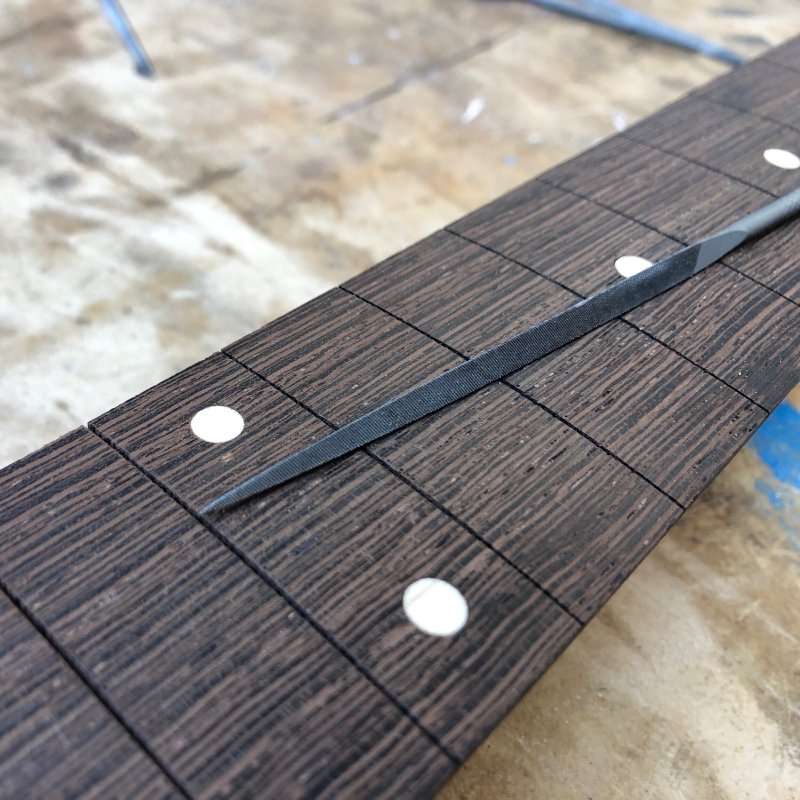
I first did this technique on the cigar box guitar, and it helps let the frets find their home in the slot a little easier. The needle-files in Makespace were a little abused for this task, so Graeme kindly brought in a set and I took them for a test drive and picked a couple that seemed right for this job.
Given I was sat down with this neck I also used a weird chisel I acquired a while ago to cut the slot for the nut:
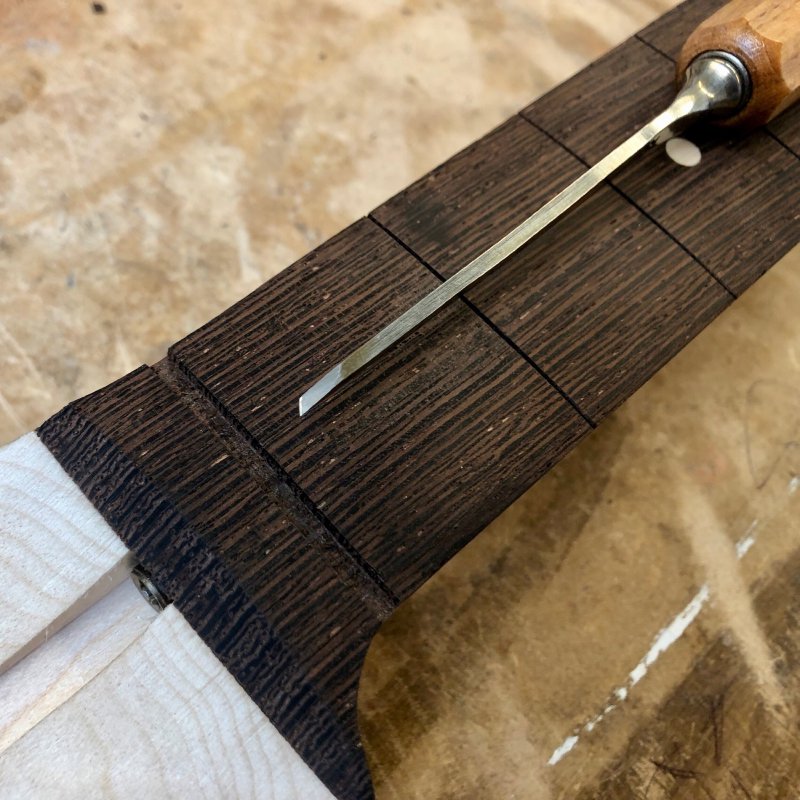
The weird shape of the edge makes it nice for this kind of work, as I can put it against one of the two slots I’ve sawn to define the sides of the slot, and let that guide the blade. However, its odd angles make it a pain to sharpen. Workshop regular Stephan encouraged me to just give it a gentle rub with a diamond stone, and that did wonders, though I’m not sure you can get away with that indefinitely.
Phew, what a week. This coming week I fear will be a quiet one as I try get back on top of contract software work delays due to a combination of laptop death and filming. However I’m sure I’ll find some time in the workshop to move things a little forward given I’m now definitely behind where I had hoped to be on the commissions. I was already a bit behind due to the new Makespace bandsaw taking a couple of weeks longer to set up than hoped, and whilst I was hoping to catch up, laptop death has put me behind again. Still, no point getting down on that - these things will happen, and I just need to find what time I can and keep moving things forward.