A fortnight out the shop
Published 16 Feb 2020
Tags: orange surf, pheonix offset, red rocker, the green tiger
Last week I didn’t manage to get my week notes posted thanks to being waylaid by Storm Ciara as I drove up to Glasgow and back - never before have I had to just stop driving and check into a motorway services hotel because the weather was just too bad to keep driving. But the trip back home was worth it as I got the pleasure of hand delivering commission #10 to it’s new owner, David:
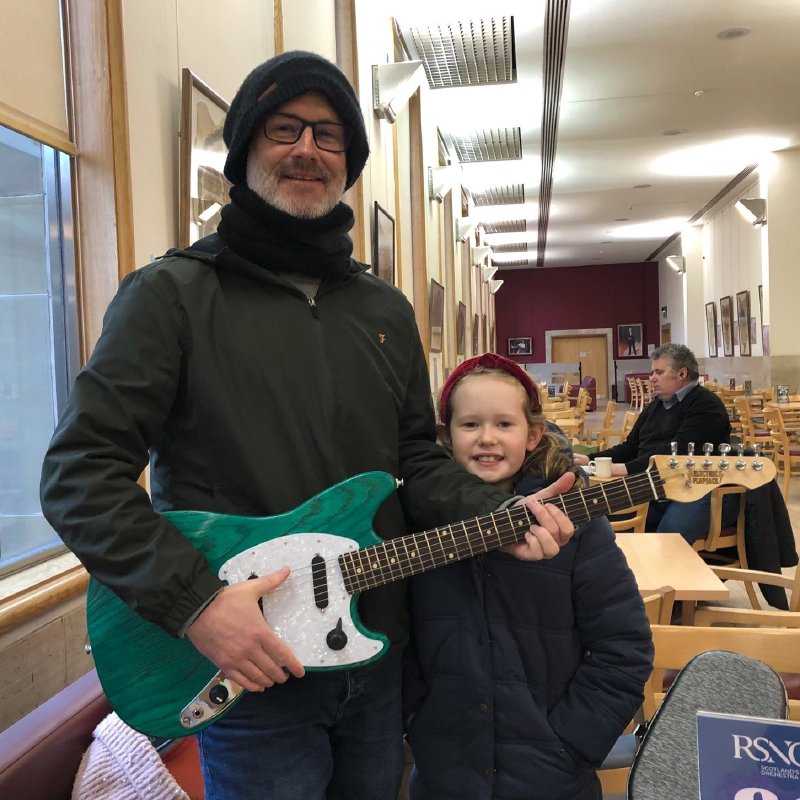
Despite the bad weather David and his daughter made the trip over to Glasgow to meet me and the guitar, which now has a name, thanks to David’s daughter: the green tiger :)
Due to incoming snow, and that I needed to head back to Cambridge that day, we didn’t get too long to chat, but after such a struggle with this build it was nice to be able to thank David for his support in person. David plays pub gigs regularly with his bad, so he’s promised to send action shots in the near future!
Whilst up in Glasgow I stayed over with my friend, who is also called David, and also has an Electric Flapjack guitar! Dave’s guitar is a tele I made for him, which I referred to as the Red Rocker as I built it, that was the third guitar I built. It was interesting to contrast build #3 and #10 in my mind, and I was pleasantly surprised by how well #3 stands up.
Yes, I’ve come a long way as a builder, and I understand what I’m doing more and why I’m doing it, but by no means is #3 a rough approximation of a guitar - it’s definitely a good guitar of which I’m still proud. Mostly I was expecting the neck to feel not as good as it did, but I think I must have really lucked out on this, the first neck I made by hand: the fretboard edges are well defined rather than rounded over as I do today, but don’t feel too sharp in the hands, and the fret ends are nicely rounded out the way. I think the only think I’d really change is I’d carve the nut a little better these days. But otherwise, it was nice to get to play this guitar and enjoy it for what it is.
With commission #10 out the way, and I’m still not yet into my new workshop, I’ve been knuckling down with some non-guitar software contract work to try top up the bank balance a bit. I’ll be moving into the new workshop soon, which means I’ll start paying rent on that soon, and I’ve finally ordered a workbench for the move, so I have a bunch of expenses I need to get paid.
As such, I guess a reminder that I have two stock guitars for sale that I would like to find new homes for - The Pheonix Offset:
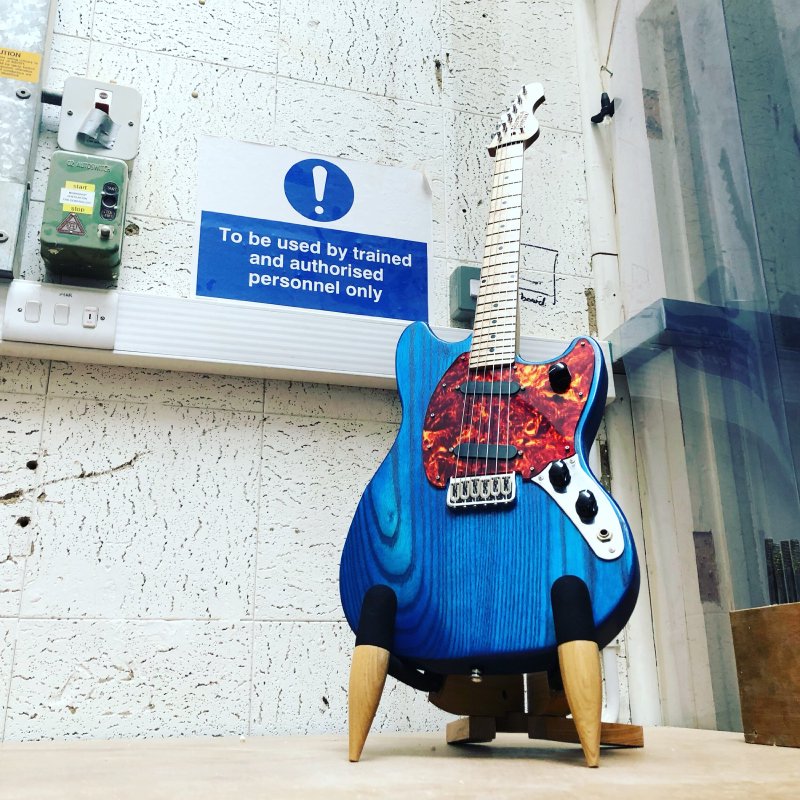
and The Orange Surf:
I’m particularly sad that no one has snapped up The Pheonix Offset, as that’s such a beautiful guitar and it’s sad to see it just sit in a case.
I’ve had these up on Reverb for a while, and that just didn’t seem to garner much interest, so I’ve taken that down for now as I try to figure out a better approach - I suspect just a squarespace store on this site. There were up for £1500, but if you can make me a reasonable offer then I’d be happy to consider it, as I could do with both the space and the money!
On the workbench front I finally pulled the trigger on a Sjobergs’ Nordic Plus, which is their high end hobbiest workbench. I had been talking to Emir, a professional workshop furniture builder based down in Ashford, about getting one of their solid workbenches. The price for my exacting specification was quite reasonable, but the delivery times were 6 to 8 weeks, and I wanted to move forward quicker than that unfortunately. I’ll have to plan better next time I need a workbench! Still, if you need a workbench (or indeed a harris loom!) then I do recommend giving them a bell.
Technically the closest Sjobergs workbench to the Emir one I spec’d was the Scandi Plus, which is their professional tier workbench, but that’s about a third as much again as the Emir quote, and whilst lovely, is a bit out of my budget right now. Given I’m not making cupboards or doors, I suspect for guitar building I’ll get by with the Nordic Plus just fine. I suspect that’ll not turn up until the week after next, so I imagine it’ll be early March before I’m back in the workshop proper.
I went for the option with storage, as I’ll need somewhere to keep all my tools neat and tidy, as I’ll be in a shared workspace.
As I’ve often mentioned, one of the nice things about the guitar building community is just how generous they are, and its something I’ve benefited from many a time, and so I’m always keen to return the favour when I can. Last week I got to help Matt of Fidelity Guitars speed up his production flow by helping him laser cut some pick-guards in Makespace:
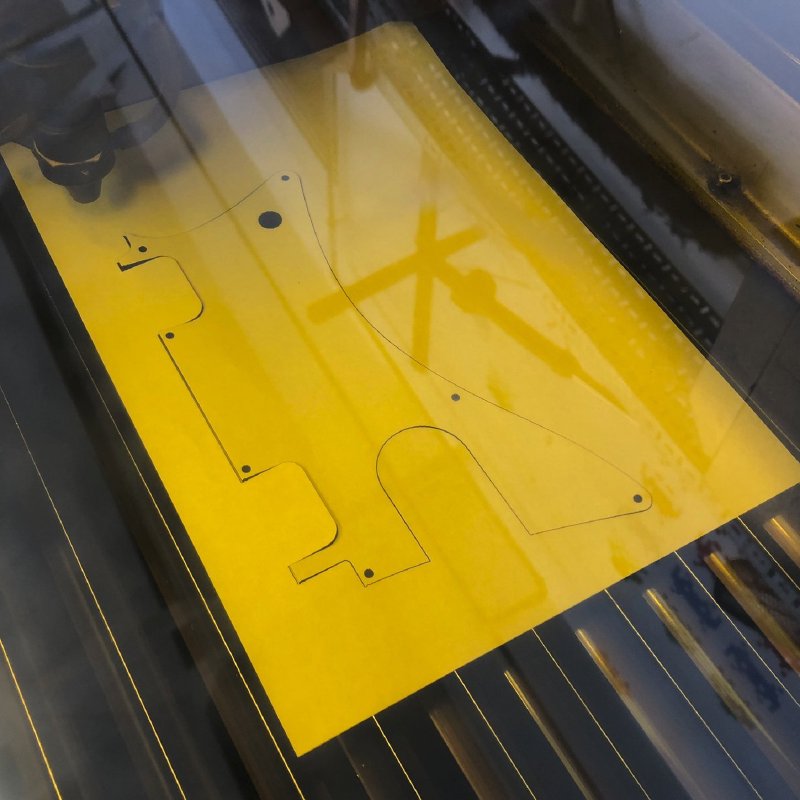
Getting the pick-guards cut was the easy bit, but getting the design files across was a comparative nightmare. Matt uses TurboCAD, a popular budget CAD tool, for his guitar designs. Unfortunately the DXF output from TurboCAD doesn’t use proper curves, rather it just uses a bunch of straight line approximations, which in certain areas were too low resolution, ruining the curves in places, and then in other areas it had made very nice curves by having thousands upon thousands of short lines, making importing the file into Fusion 360 at best slow, at worst crashy.
In the end Matt found a work around, which was to extrude the 2D design in TurboCAD so he could export it as a 3D STEP file, which kept nice curves in it, and this I could then import into Fusion 360, and re-export as DXF. Alas, our picky laser cutter doesn’t like modern DXF files, so I still had to run that through Adobe Illustrator and re-export it as an older DXF format. And we had to do this four different designs of pick-guard! No wonder us software engineers have a bad name.
Still, in the end we managed to make light work (ho ho, there’s a pun in there) of cutting Matt’s pick-guards, doing so much faster than he could have done on his CNC Router:
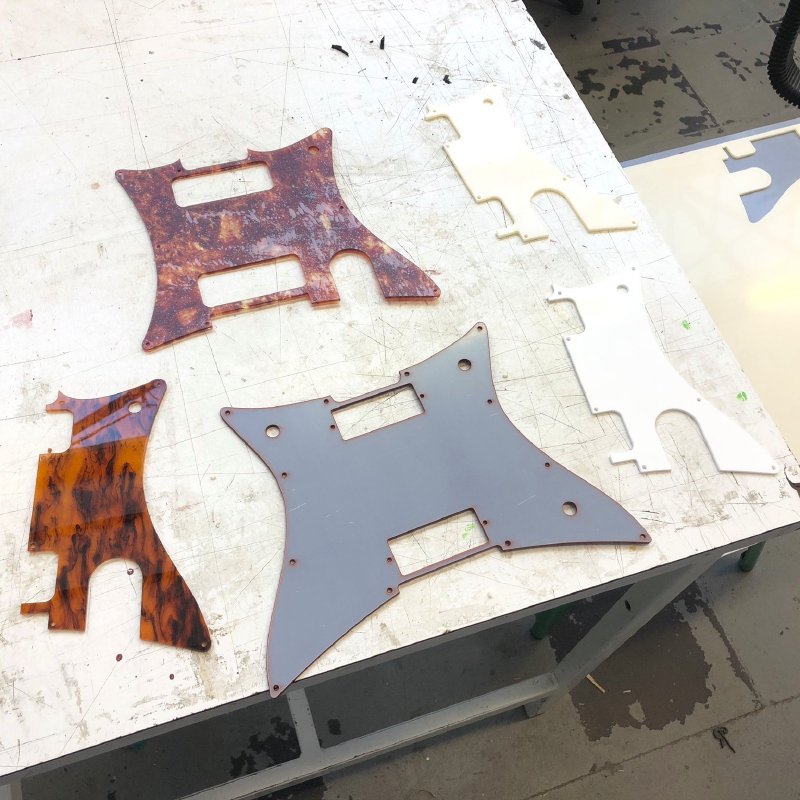
You can see these installed on guitars over on the Fidelity Guitars instagram account.
And of course, now that we’ve done all the file format hoping once, next time Matt needs some pick-guards cut (in acrylic at least) we can get them made in minutes rather than hours.
What will I do when I’m back in the shop? Well, I have two guitars that are half built that I need to get finished. First up is the final offset commission that I got a while ago for a friend that I need to complete, and there is the corvette experimental build that I’m making also:
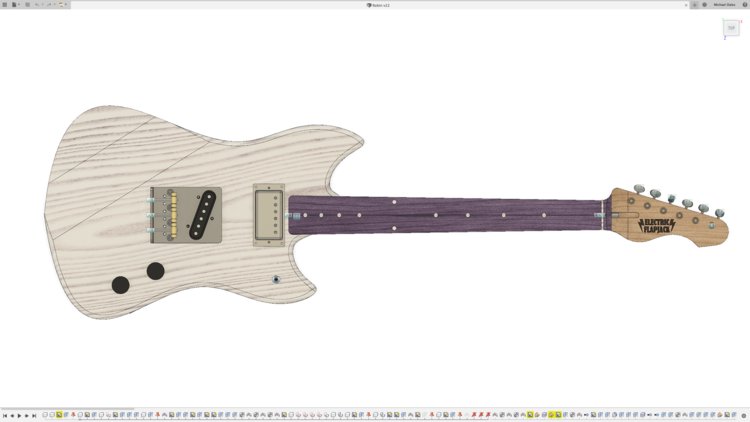
However, I also realise I need to make a third guitar in the near future: a better demo guitar. Whilst I’m proud of the guitars I do currently have sitting around, they are all based on the same 24" scale length offset design, and whilst people make nice comments about the craftsmanship, I think if you’re used to playing longer scale instruments (i.e., 25.5" scale Fenders) you don’t necessarily take to the smaller instrument - at least that seems to be the case to date when I’ve got feedback on them from potential customers. Thus I need to build something that people can identify with more. As such, for the first time in far too long, I’ve been trying to actually design rather than make:
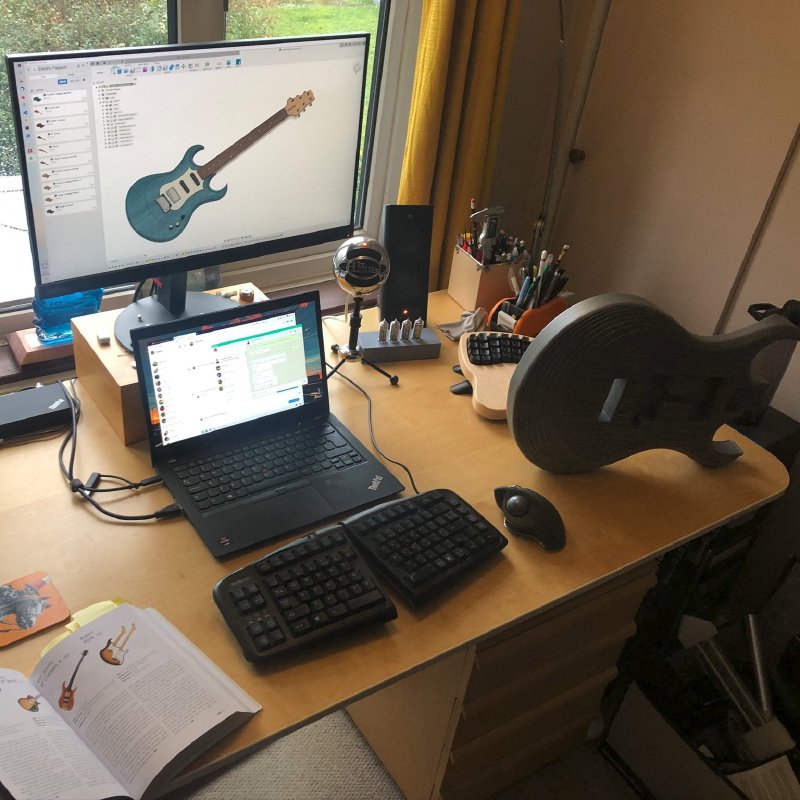
I’ve been playing with the designs I made a year or so ago, and re-reading 1001 Guitars To Dream Of Playing Before You Die, which is a great inspiration for guitar designs (and a reminder that not every guitar made that people revere is a think of beauty). Over the coming week or so I’ll hopefully then come up with something to build as a demo that is both more familiar to people yet still something that is distinctly mine.