Pre-xmas week in the shop
Published 23 Dec 2017
Tags: blues deluxe, soldering, tuners
The week started early on Sunday, with a visit from Tristan Dales of IKARI brining his Chuncaster in for a little tune up. I wrote more about this already on the blog, so I won’t go into it much again, other than to observe again that is was nice to see the Chuncaster again, and Tris as ever amazes me with his playing.
Next up I found I had a bad solder join on the tone pot in Guitar #3, so I fixed that. I failed to spot this first time around in part due to the test amp I have in the workshop not being the best and the Makespace workshop not being the quietest at times. Although the Orange Micro Crush amp for 40 quid is not bad, particularly has it has a tuner in it, the speaker really isn’t that great, and it seems there’s much better things out there since I got this. For example, the Boss Katana Mini has been getting great reviews, so I might look to upgrade my workshop amp in the new year.
Speaking of tuners, as a random aside, I got the TC Electrics Polytone clip-on tuner at the start of this year, and whilst it’s very good as a player, a clip on tuner is an essential as a luthier. Clip on tuners work by detecting vibration in the guitar body, so when you have a solid body guitar without electronics that is too quiet for microphone based tuners and can’t yet be plugged in to an electronic tuner, the clip-on style comes into its own and is in my mind essential workshop kit. There’s others out there, but the TC one is quick, accurate, and convenient, so I can’t recommend it enough.
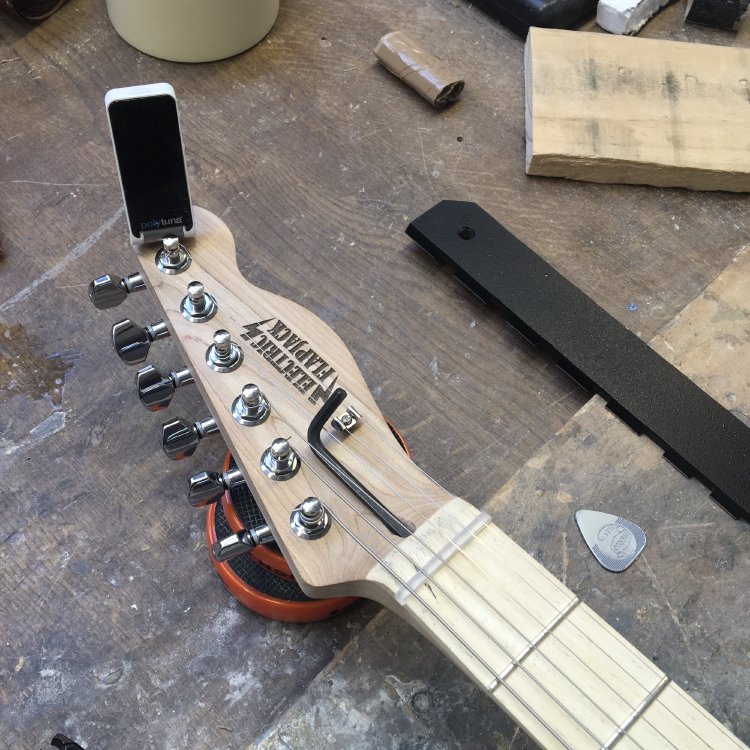
I spent yet more time finishing off the amp design in Fusion, and now I’m in a position where I can start cutting the wood after a final review. Traditionally amp cabs are made from birch plywood for it’s strength and resonance properties, but it’s really quite expensive, so not something you want to waste. So I’ll start with a practice run on MDF to get the gremlins out before doing anything in birch ply. That said, my daily player guitar is made of basewood as I got the cheapest guitar body I could for my first experiment in building a guitar, on the assumption that as someone who hadn’t done woodwork in over a quarter century I was bound to destroy it. But because I was careful (and perhaps lucky) that cheap body made it all the way to the final build and I still play that guitar almost daily.
I started on the electronics on Guitar #4, which will be a Tele Deluxe style with P90s rather than humbuckers. If Guitar #3 represents a refinement of all I learned from the preceeding guitars, Guitar #4 represents trying to start branching out into new areas. Small steps, still being a t-style of sorts, but the manufacture is more based on my own methods, it has distinctive looks, and I’m really excited to try these House of Tone P90s that I got voiced for this guitars intended use as a blues player. Overall I’m hoping this guitar will have a clear Electric Flapjack stamp on it.
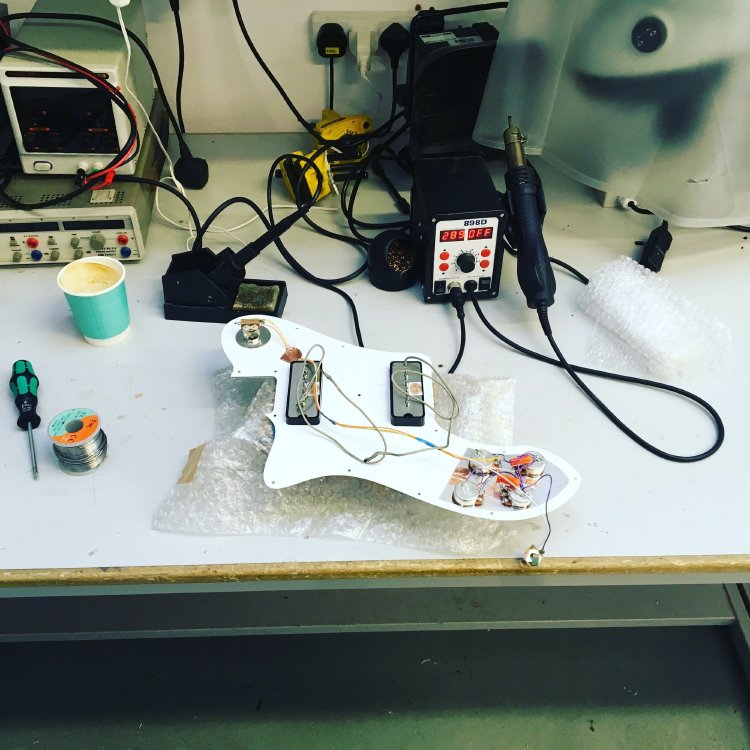
The soldering is all done, but I hit a snag printing the nut for this guitar which is now a blocker on completion. I’ve had real bad luck using the Form One to print nuts, with a less than 50% success rate. My theory is that because of the nut’s narrow profile, the print base doesn’t adhere properly at the start of the printing progess, so I’ve tried printing them out in pairs to give the overall model a wider profile. Based on my most recent run this appears to have solved the base problem, but the supports failed to come out this time, so I’m back to debugging this. I may have to give in and actually file a regular bone nut if I can’t solve this, but I really like the clear nut I printed for guitar #3 and I’m taken with the idea of a black nut on #4, so I’ll persist a little more before giving up.
With xmas coming up I’m not sure how much I’ll get done in the coming week, but I hope you all have a great festive break, and week notes will come back hopefully in the new year!