A week in the shop
5 Feb 2019
Tags: electronics, the dandy warhols, the-clydesdale
At the end of last week I had successfully, after a bunch of failed attempts, cut out a pristine pick guard for The Clydesdale offset guitar, so I started this week by bringing together all the bits of the guitar and working on the electronics. First was just to get all the final bits together onto the guitar. Here it is from the front:
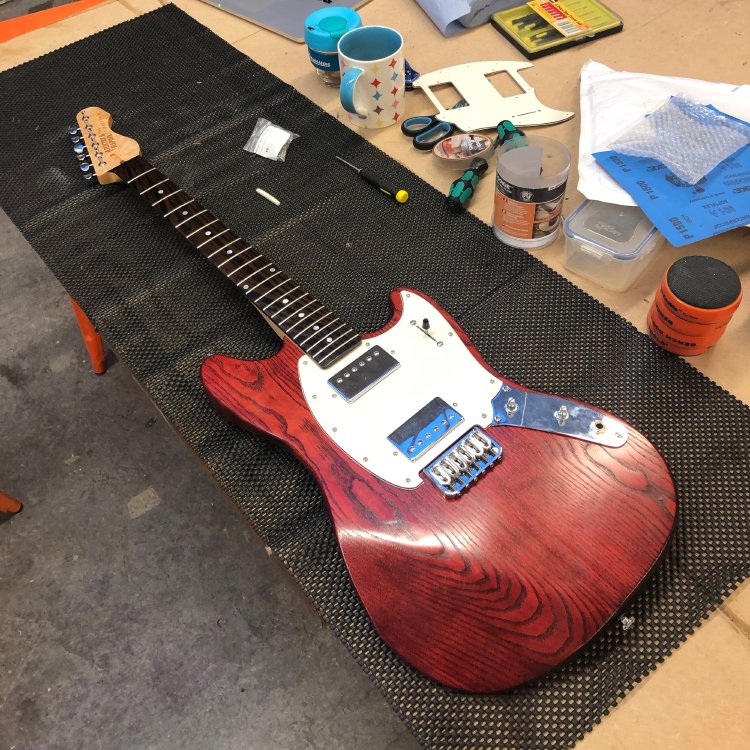
and from the back:
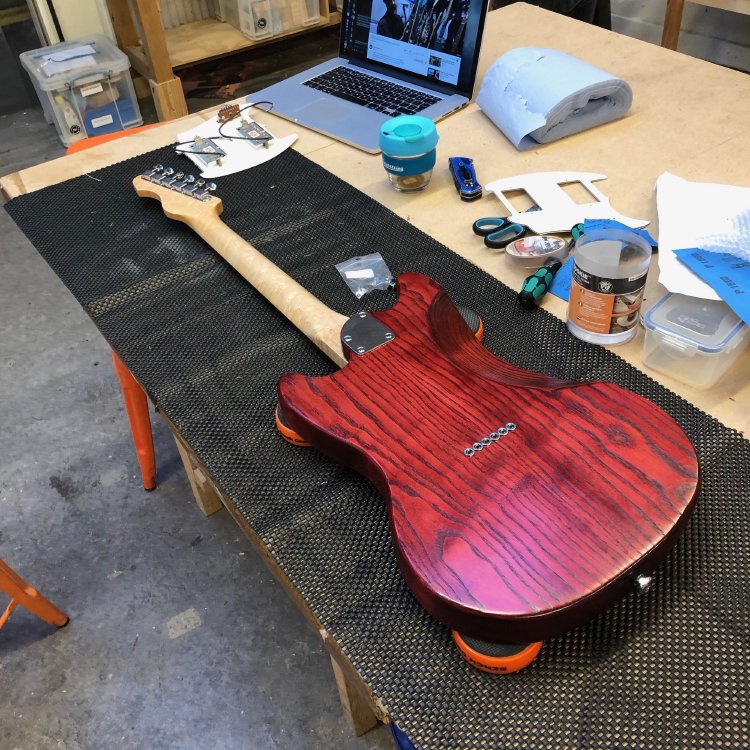
It’s looking lovely. I did a quick rough shaping of the nut, but that’s one of the last bits to do at final setup time, once the electronics are done and we’re just dialling in the final playability.
The electronics took me longer than it should of because I have a tendency to leave as much wire on the pickups etc. as I can, just in case someone wants to re-purpose the pickups later or other such events. However, there really isn’t much room to manoeuvre in this guitar, so I ended up effectively wriring everything up twice: first with lots of spare wire, and then having realised I didn’t have enough space in the body cavities for all that wire I then had to unsoldered everything, cut things to a better size, and put it back together again (and thankfully it all fit nicely this time). Partly the limited space is down to the mustang not having much room under the metal control plate combined with using push/pull pots to let the player switch the pickups between humbucker and single coil modes - fender really didn’t have this in mind for this kind of guitar. The other reason for the lack of room was my own doing: in an attempt not to remove too much wood from around the pickups (to leave the body being solid rather than hollowed out) I’d left not a huge amount of room when I designed the space behind the pick guard: in retrospect I should have left more room. Still, we got there in the end.
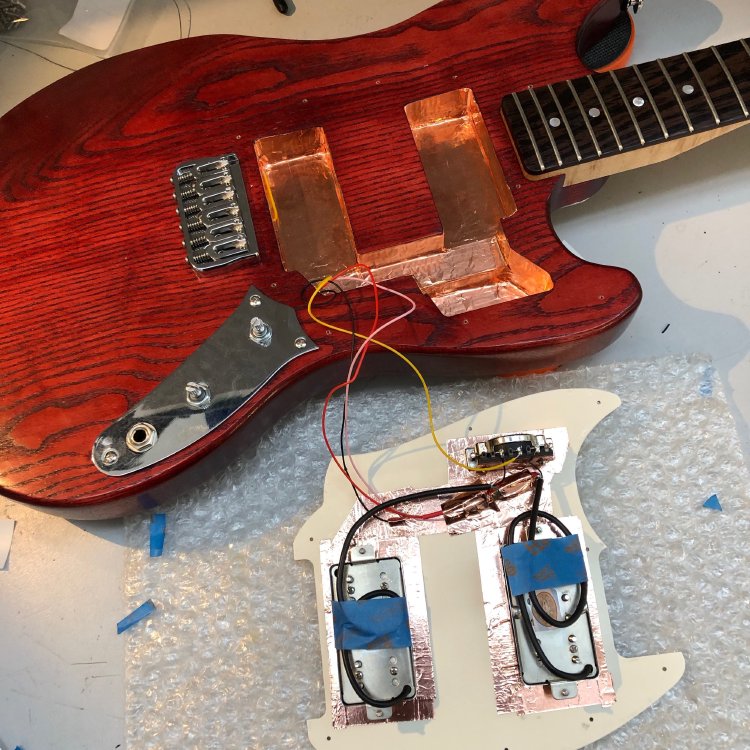
Electronics done I could finally string up the guitar and see how much setup was needed. This is where I discovered that the neck is sitting too high for the fixed bridge on this guitar, and the strings were buzzing on the frets even with the saddles extended as high as they’d go.
This hadn’t been an issue on the prototype offset, which used the dynamic vibrato bridge system, and that bridge naturally sits quite a bit higher than the hardtail bridge the customer wanted on this build. I did have a look at Fender’s Mustang guitars with a hardtail bridge, and they do tend to have them with the saddles set really high. In the photo below you can see quite a lot of screw under the saddles on the bridge, more so than I’d expect on say a Strat.
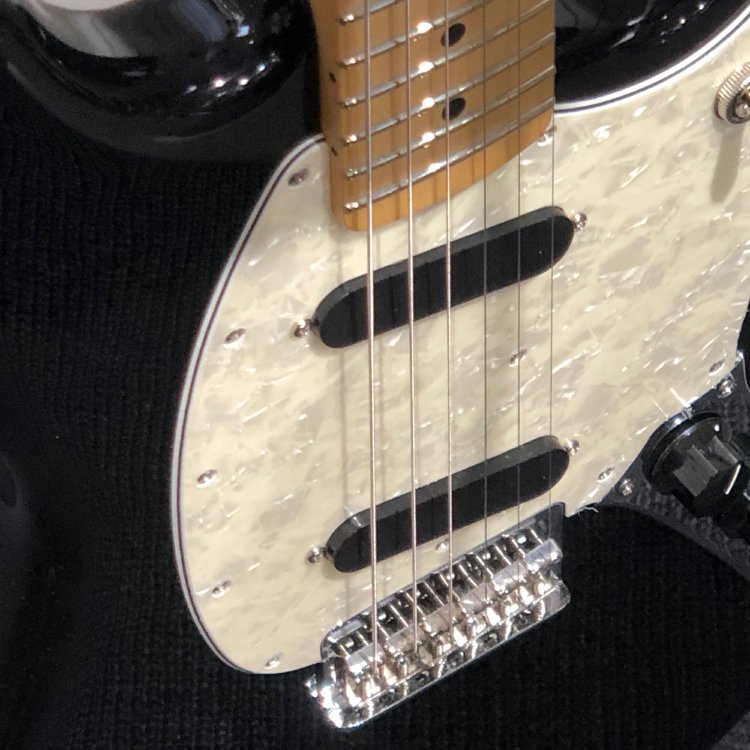
However, on The Clydesdale it’s just a bit too much: I think I need to take a millimetre or so out of the neck pocket to get things sitting comfortably. So this week I need to take the neck off and with the hand router remove some wood from the neck pocket using the hand router and a short follow bit. I’ll need to make a small jig to let me use the hand router over the finished body without scratching the surface, but I’ve actually done this before on The Chuncaster t-style I made early on, which had a similar problem.
The frustrating bit about it is I find out these sort of things at this late stage in the build: ideally I’d string the guitar up early on before doing any finishing. However, with Fender style guitars this is something I’m generally reluctant to do, for two reasons. Firstly, when you assemble the guitar and put it under tension by stringing it up you’ll find the metal parts like the tuning pegs and the neck plate will mark the wood as they press into it. Doing this after you’ve oiled the wood makes such marks less pronounced as the oil toughens up the wood’s outer surface. The second reason I try to avoid it is for string through guitars like this one I’d need to put in the ferrules on the back which then I can’t typically not remove, but would like to not have there when I do the finishing. Hence why I only tend to find out now that I need to adjust heights etc. after it’s finished and I then need to be very careful about such adjustments.
Mostly all this is down to a lack of experience: if I made a lot of guitars I’d be better at predicting things like this before we get this far into the process. But it is also useful learning for my own guitar designs. I think with a bit of tweaking I can design the guitar in such a way that it won’t notably mark when assembled and put under tension before finishing (e.g., using recessed screw ferrules to hold the neck rather than a Fender style neck plate).
Anyway, I have a fun week ahead of me getting the guitar adjusted so it’s a musical instrument rather than a pretty bit of art.
The rest of the week was taken up with some sudden contract work, so I didn’t do much else in the shop. I did manage to pick up some bits for the other projects I’ve got going. I was in London for a gig (see below), so I swung by GuitarGuitar in Camden and picked up a new pedal board PSU (another Walrus Audio Aetos in the end, given I know it and have been happy with it), which means at some point this coming week I can finally assemble my pedalboard prototype and start (literally) stress testing it by mounting all my pedals on it and stomping on it bunch.
I also managed to raid the spares trove in Makespace and find the correct capacitors for the fuzz pedal I built last week.
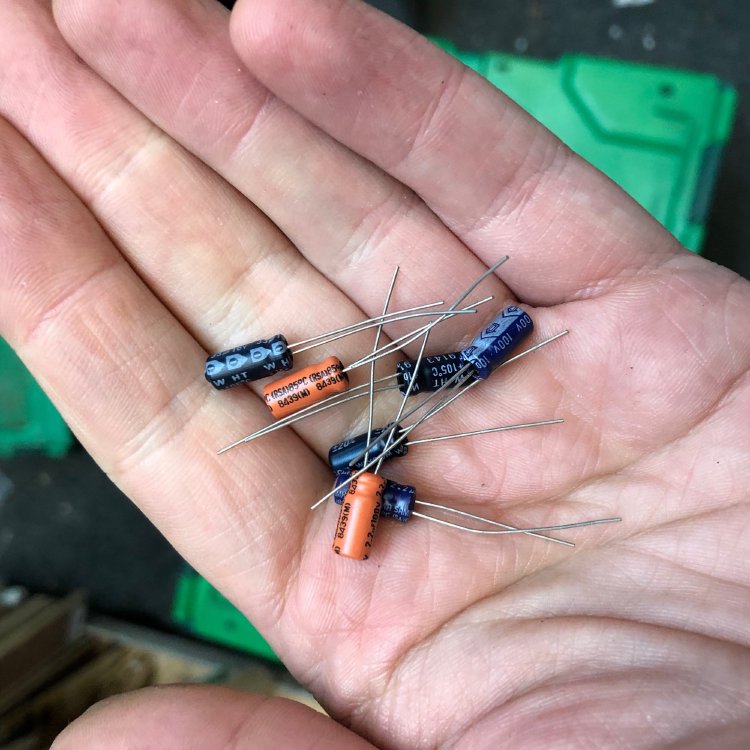
Putting these caps in place solved the sound drop issue I as experiencing with it, and now I have that classic fuzz tone. At some point I can now take this from breadboard to some veroboard (or if I find time, a custom PCB via Eagle) and mount it on my pedalboard and have it in regular rotation.
I did get to visit another workshop briefly: I was up in Liverpool at the weekend, so I finally made good on a promise I’d made in autumn last year (where does time go?) to run the Fusion 360 tutorial course I run regularly at Makespace for the DoES Liverpool community. The turnout was less than we’d hoped, I suspect due to the inclement weather, but we had enough people to keep me busy for the full duration, and feedback seemed positive.
It was nice to meet a different set of makers; DoES has different vibe to Makespace, and I met people working on things no one is working on at Makespace. For example, I met one chap who has been using 3D printing to make moulds for casting jewellery, and was interested in Fusion 360 so he could start using their CNC Router to make moulds by milling out material - very interesting stuff.
From a personal perspective, it was also nice to chat to Adrian McEwen, one of the founders of DoES and someone I’ve had the fortune to know for a while. Long before I set out on this, Adrian’s been forging his own path in trying to work on interesting and meaningful projects between bits of contracting and is very familiar with the trials of making physical things, so it was nice to have someone to compare notes with given all the issues I’ve had over the last year. Adrian has also been doing weeknotes, so if you’re interested in seeing what he’s been up to, you should check his notes out.
I also managed to go see one of my favourite bands, The Dandy Warhols, who were playing in London. Hard to believe they’ve been going 25 years now (again, where does time go?). They did a great set, and I love how The Dandy’s do their shows: there’s no fake encore, just one bountiful set filled with a mix of things from their most recent album and spanning a good chunk of their back catalogue. Also, and I’ve not seen any other headline band do this, they present themselves as a group of equals: all four members are in a line at the front of the stage, including their drummer Fathead; it’s a small thing, but I think makes a big statement about them being a group of equals, and not just a singer and some musicians.

Of the support bands, I really loved the 60s psychedelic surf sounds by Juniore. You should check there stuff out on their bandcamp page if you’re at all into that sort of thing.